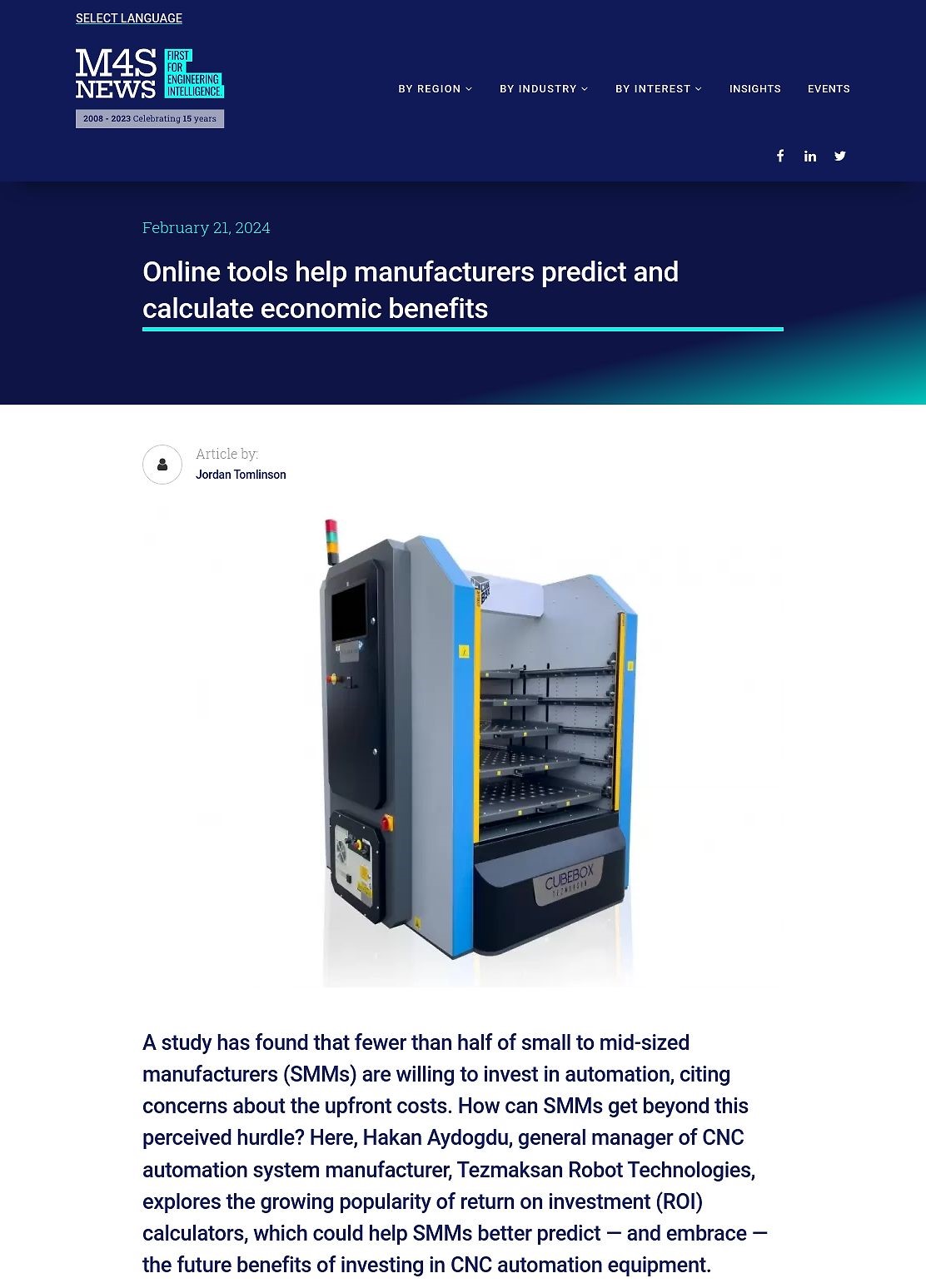
Online tools help manufacturers predict and calculate economic benefits
A study has found that fewer than half of small to mid-sized manufacturers (SMMs) are willing to invest in automation, citing concerns about the upfront costs. How can SMMs get beyond this perceived hurdle? Here, Hakan Aydogdu, general manager of CNC automation system manufacturer, Tezmaksan Robot Technologies, explores the growing popularity of return on investment (ROI) calculators, which could help SMMs better predict — and embrace — the future benefits of investing in CNC automation equipment.
In today's rapidly evolving industrial landscape, the integration of CNC automation has shifted from being a ‘nice to have’ to a strategic necessity for manufacturers. Deloitte's 2024 Manufacturing Industry Outlook report underscores this trend, with 86 per cent of surveyed manufacturing executives acknowledging that smart factory solutions will be the primary drivers of competitiveness over the next five years.
While larger companies are leveraging automation, SMMs have been more hesitant. Less than half said they were willing to invest, according to a survey by the Smart Manufacturing Institute (CESMII) and the Society of Manufacturing Engineers (SME). A major concern is the perceived upfront investment of automation — as written in Harvard Business Review, “the robotics industry has traditionally been dominated by large, complex machines that require significant up-front investment and in-house expertise to keep them running.”
Fortunately, this is changing as industrial robots and automation systems become smaller, more modular, and affordable. Another change is the growing popularity of return on investment (ROI) calculators to accurately predict the benefits of CNC automation. ROI, in essence, is the time required to break even on an investment, considering both costs and benefits. Let’s look at how ROI is calculated for CNC automation.
Predicting returns
Calculating the ROI for CNC automation involves a systematic approach, starting with the identification of goals and objectives for implementing the automation in the first place. These objectives may include increased production efficiency, reduced labour costs, improved quality or enhanced production capacity.
Next, manufacturers should apply a comprehensive cost analysis, encompassing the initial investment and ongoing operational costs. The former includes purchase costs, installation, training and any necessary infrastructure changes on the factory floor. The latter considers maintenance, energy consumption, and additional expenses related to running the CNC equipment.
Estimating labour cost savings is a pivotal step, as a crucial benefit of automation is the reduced need for manual intervention in the production process. Forbes highlights that automation can potentially free up to three work hours a day, or 360 hours work a year, leading to substantial labour cost savings. Aside from reduced labour hours, there can be fewer production errors caused by human mistakes.
Modular cell
Through such calculations, automation equipment can be used to its optimal capability. Take for instance Tezmaksan’s CubeBOX system, a modular cell that can be easily integrated into any production line. The CubeBOX is compatible with all CNC machines available on the market, including all types of CNC lathes, machining centres and grinding machines. It seamlessly integrates with the existing robot operations, eliminating the need for extensive modifications or customisations. This compatibility feature simplifies the implementation process and minimises downtime during the installation phase.
Offering 24 hours operator-free operation, the core advantage of the CubeBOX system also lies in its ability to work non-stop. Ensuring uninterrupted production even during night shifts, this continuous operation leads to a remarkable 50 per cent increase in night shift efficiency compared to traditional setups that rely heavily on manual labour for CNC machine tending.
Beyond labour cost savings, manufacturers must also consider the impact on production capacity, quality improvements, downtime reduction, time-to-market enhancements and potential revenue increases. After all, faster and more efficient CNC processes can contribute to increased production capacity, reduced downtime and faster turnaround times. Companies can use different methodologies to determine this impact.
Different approaches
The actual ROI calculation involves subtracting operational costs from the net benefits (savings from labour, reduced downtime, increased capacity, quality improvements, etc.), multiplying this by 100, and then dividing by the total cost (initial investment plus ongoing operational costs).
One methodology is the payback period, or the time taken for the investment to be recovered from net cash inflows. This is a straightforward way to evaluate how quickly a company can recoup its investment, calculated by dividing the amount of the initial investment by the annual net cash flow. A shorter payback period is generally preferred as it indicates a quicker ROI. Payback period is useful for assessing risk associated with the investment, especially in industries with rapid technological changes.
Another methodology is net present value (NPV), which accounts for the time value of money by discounting future cash flows to their present value. To calculate NPV, you need to determine the cash flows for each period of the investment or project, discount them to present value, and subtract the initial investment from the sum of the project's discounted cash flows. A positive NPV means the investment is expected to generate value, giving a more accurate representation of the investment's profitability.
Our next methodology is the internal rate of return (IRR), which compares the investment’s inherent rate of return to the required rate of return. If the internal rate of return (IRR) for Proposal A exceeds the company’s cost of capital, which represents the required return on investment, the project is generally deemed acceptable.
In the case of Proposal A, requiring an initial investment of £100 million today and yielding a return of £121 million in precisely two years, the IRR is calculated using the formula: IRR = (end amount / starting amount)^(1/n) - 1. Plugging in the values, with the end amount as £121 million, starting amount as £100 million and a time delay (n) of two years, the resulting IRR is ten per cent.
Key variables
Online ROI calculators are becoming more popular throughout industry. They include Tezmaksan’s own online ROI Calculation tool. A range of important variables can be entered into the tool — the investment cost, total expenses, the number of CNC operators, expected working days per year and hours per day, labour expenses, the price of the workpiece, insurance premiums and more. Based on these variables, users can calculate a definite ROI figure for the year.
To make the analysis more robust, manufacturers should perform sensitivity analysis to understand how changes in key variables — such as production volume, labour costs — impact the ROI. Additionally, it's crucial to consider intangible benefits such as improved employee morale, increased competitiveness and enhanced market reputation.
Calculating the ROI for CNC automation requires a meticulous analysis of tangible and intangible factors. Regularly reviewing and adjusting calculations ensures accuracy and relevance to the evolving business environment. By embracing automation strategically, manufacturers can not only improve their bottom line but also position themselves competitively in the ever-changing market landscape.